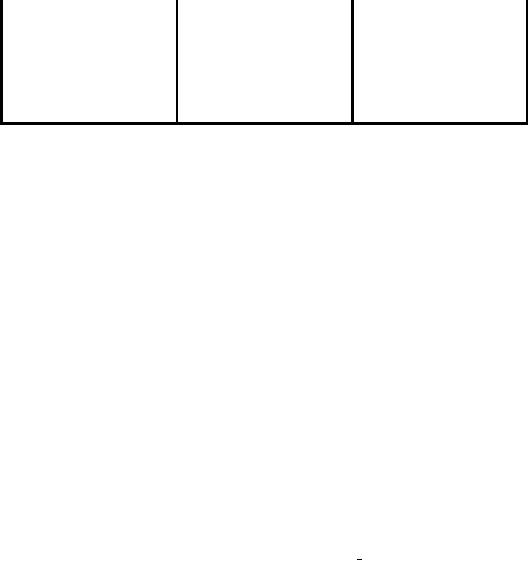
MIL-DTL-81984C(OS)
501-800
30
10
801-1300
35
10
1301-3200
40
10
3201-8000
50
10
8001-22000
75
10
4.5 Tests.
4.5.1 Ignition element verification. Verification shall be provided that the ignition element used were
certified and accepted in accordance with the requirements of 3.5.
4.5.2 Smokeless powder, condition. Smokeless powder shall be inspected in accordance with the
applicable paragraphs of OP5. Evidence of decomposition shall because for rejection.
4.5.3 Visual examination. All cartridges shall be visually examined. Cartridges having any of the
defects of 3.10 shall be cause for rejection.
4.5.4 Bridge circuit resistance. Conformance with the bridge circuit resistance of 3.7.1 shall be
ascertained on all completely assembled cartridges by means of a test circuit which limits the bridge
circuit current to not greater than 25 milliamperes. A safety chamber with an interlock switch shall be
used to protect the operator during the application of current. A suitable instrument which is known to
be accurate to within 1 percent in the range of resistance specified shall be used to determine whether or
not the requirement is being met. Units which fail to meet the requirements of 3.7.1 shall be cause for
rejection. The results of bridge circuit resistance measurements shall not be affected by resistance of the
test circuit and connector.
4.5.5 Leakage. Each cartridge in the first article or production sample shall be leak tested in a dry gas
leak tester. Cartridges which exhibit a leakage rate greater than 10 5 cc per second of air at a pressure
differential of 1 ± 0.1 atmosphere shall be considered defective. Cartridges of the first article sample
which exhibit a leakage defect shall be cause for rejection. If one or more cartridges of the production lot
sample leak, then a leak test of each cartridge purchased under contract for the lot being tested shall be
required. If a 100 percent leak test of the lot is required, it shall be at the expense of the contractor.
Cartridges which exhibit a leak rate in excess of that specified above shall be rejected (see 6.5).
4.5.6 Radiographic examination. All cartridges in the first article and production test samples shall be
radiographically examined in accordance with ASTM E1742. Cartridges having any observable
imperfections in assembly shall be cause for rejection. The cartridges shall be positioned on their sides
for the most revealing exposure. All cartridges shall be identified with serial numbers prior to
examination. The cartridge serial numbers shall be in consecutive order beginning with the number 001
in each production lot. The cartridges shall be arranged on trays or boards in consecutive numerical
order, and each radiograph shall carry a permanent identification of the cartridges displayed thereon.
The radiograph identification shall include the complete lot number, as stamped on the cartridges, and
the span of serial numbers displayed. If any assembly or loading defects are noted in the production lot
samples, the contractor must x-ray the represented lot 100 percent and submit the x-rays to the cartridge
design activity for review. Discontinuities in the serial numbers shall be identified on the x-ray.
Defective cartridges found by the vendor shall be clearly identified on the x-ray and those defectives
removed from the production lot. The serial numbers shall be pen or ink stamped on the cartridges with
approximately F-inch-high characters. The serial numbers shall be located apart from the other cartridge
markings.
6
For Parts Inquires submit RFQ to Parts Hangar, Inc.
© Copyright 2015 Integrated Publishing, Inc.
A Service Disabled Veteran Owned Small Business